Twin Chimney’s Farmhouse Renovation Project
If you love old homes as much as I do, you will surely love the story of the Twin Chimney Farms renovation project. Travis and I were honored that the homeowners, Jack and Carole Arey trusted us and Walker Woodworking to be a part of this 18-month long project. These final results of his circa 1817 farmhouse rehabilitation project are truly amazing!
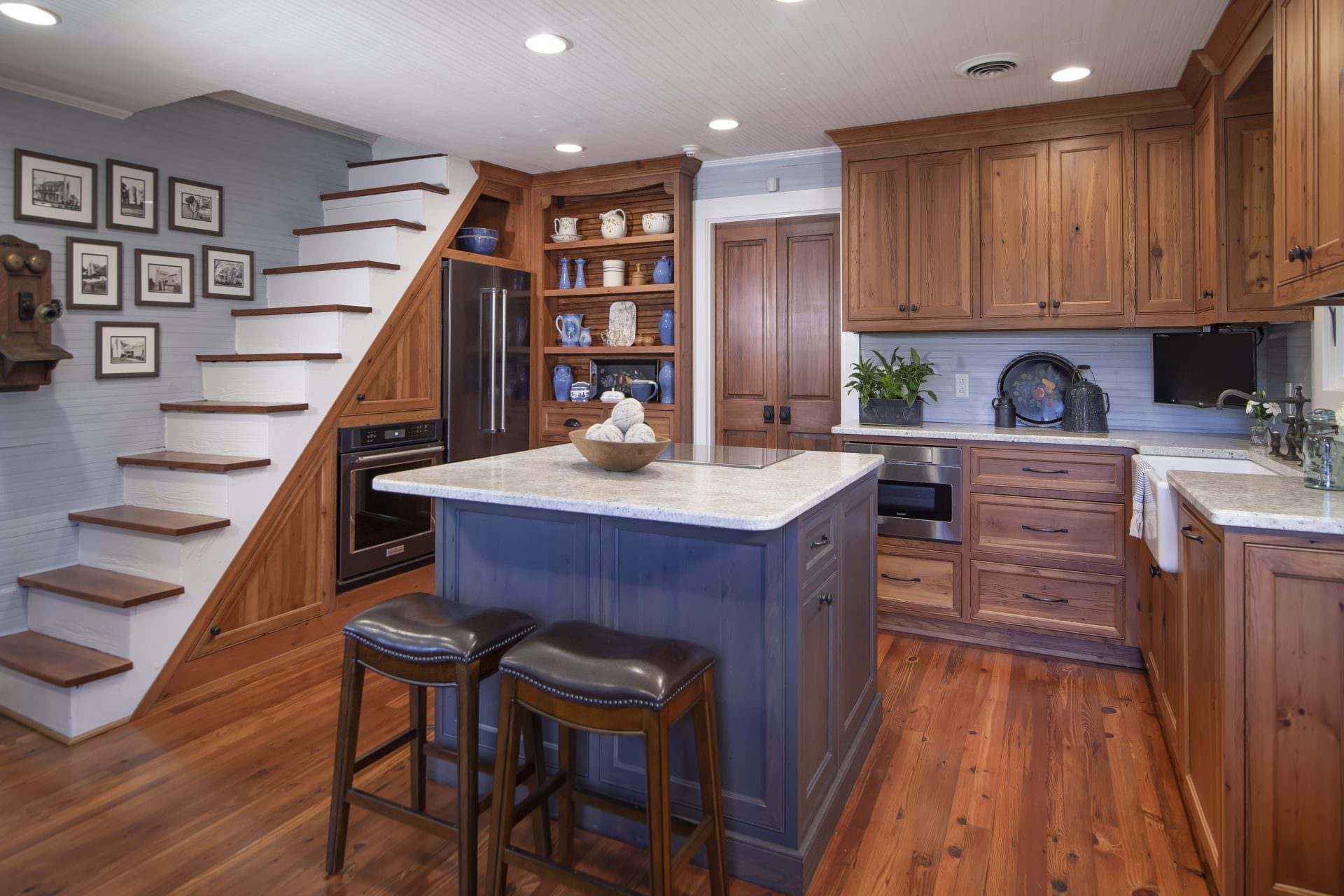
After Photo of Kitchen
Planning and Preparation
Projects like this one can be very challenging due to the time it takes to properly plan and execute the complicated details for a renovation of this magnitude. Like most homeowners, we want to wrap up projects as quickly as we can. However, we knew this assignment would take a lot of time because the details were complex and the rules were extremely strict for a historic home rehabilitation. Travis Walker, President of Walker Woodworking, and Brandon Fitzmorris, lead designer for Greenbrook Design, teamed up with Tony Brooks, the general contractor with Beam Edwards and Brooks as well as the interior designer, Wendi Gragg to see this project through to the end. We hope you enjoy this story and appreciate the craftsmanship involved to preserve the home. To skip the story and view the gallery click this link.
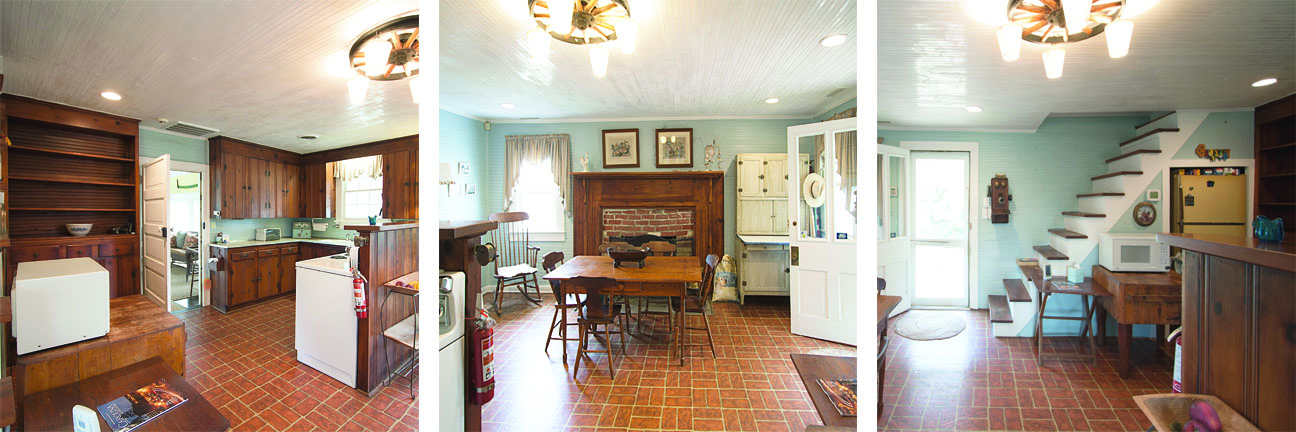
Before photos of the kitchen.
If these walls could talk, what a deep history they would speak!
If the walls of this home could talk I believe they would tell you how grateful they have been for the care and maintenance of the family that has owned this home for many years. Let me introduce you to the current homeowner, she is the great-great-granddaughter of Joesph Suttle; Meet Mrs. Carole Arey and her family history related to this home. Here’s her story:
History of Twin Chimneys
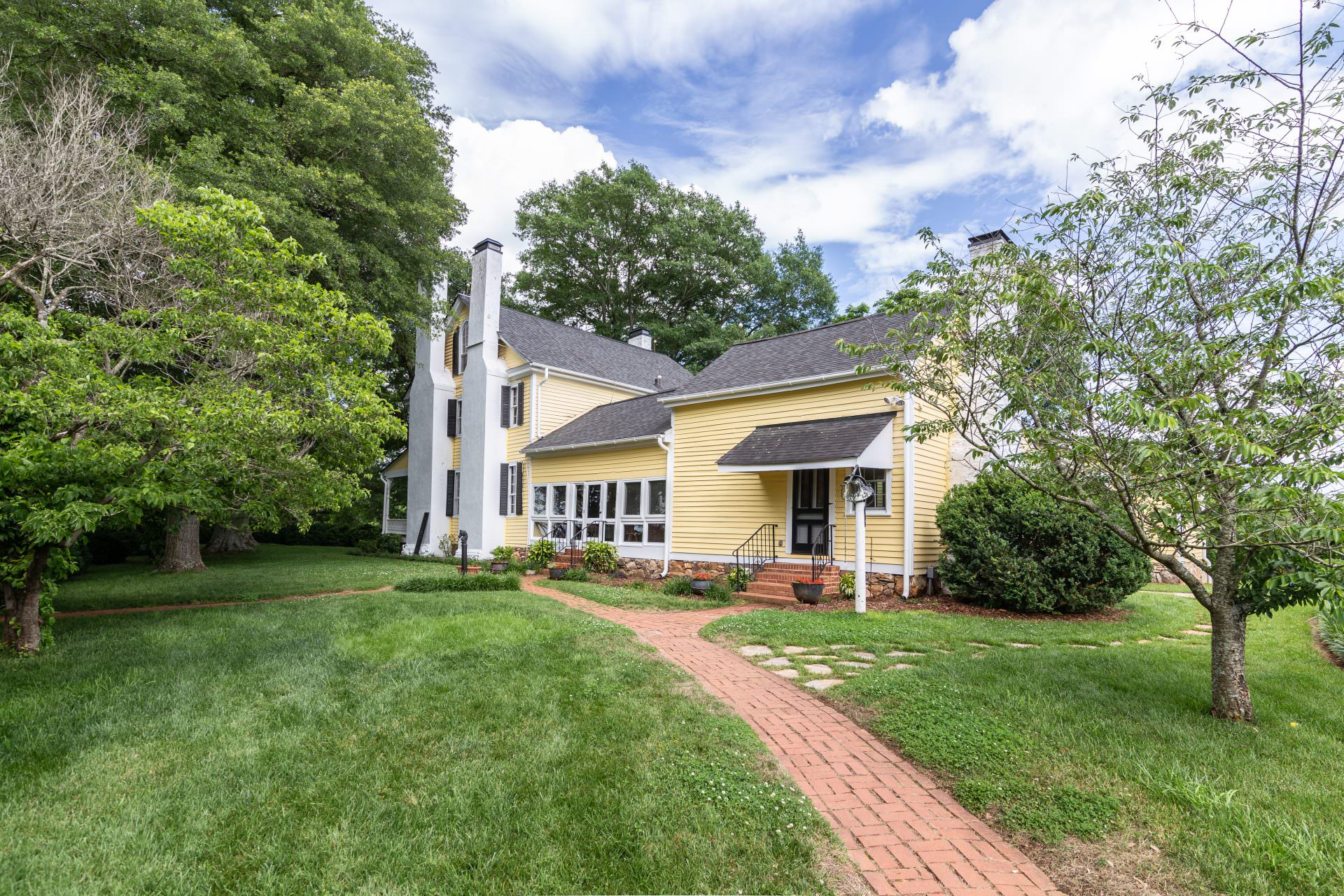
Twin Chimney’s farm, named for the Twins Chimney’s on this side of the home. There are actually four Chimney’s total in the home.
“The Joseph Suttle house, locally known as Twin Chimneys was built around 1817 for Minor W. Smith. Smith was born in England in 1784. He immigrated to Wilmington, North Carolina and then to Shelby. Joseph Suttle and his wife bought the property in 1854. Joseph Suttle died in 1861 at the age of 34. His widow and heirs sold the property in 1883. The house saw a long series of owners both in and out of the family until purchased in 1943 by J. L. Suttle Jr., a great-grandson of Joseph Suttle, and his wife Sara McFarland Suttle. It was listed on the register of ‘Historical Places” in 1980. The house is one of the best known antebellum residences surviving in Cleveland County. Included on this property is a cemetery which includes the graves of Minor Smith and his wife Jane, and of Joesph Suttle and also other decedents.
Today Twin Chimneys is owned by my husband and I William Jackson Arey and Carole Suttle Arey. Our Architect Jerry McGinnis, who we have worked with on previous projects, was invaluable throughout this farmhouse renovation & rehabilitation. “
“We appreciate every single person who worked with us on this project, we couldn’t be more pleased with the end result. Everyone that had a part in this venture was extremely patient with us and we thank you! Really, there is nothing we would change if we had to do it all over again.” ~ Jack & Carole Arey
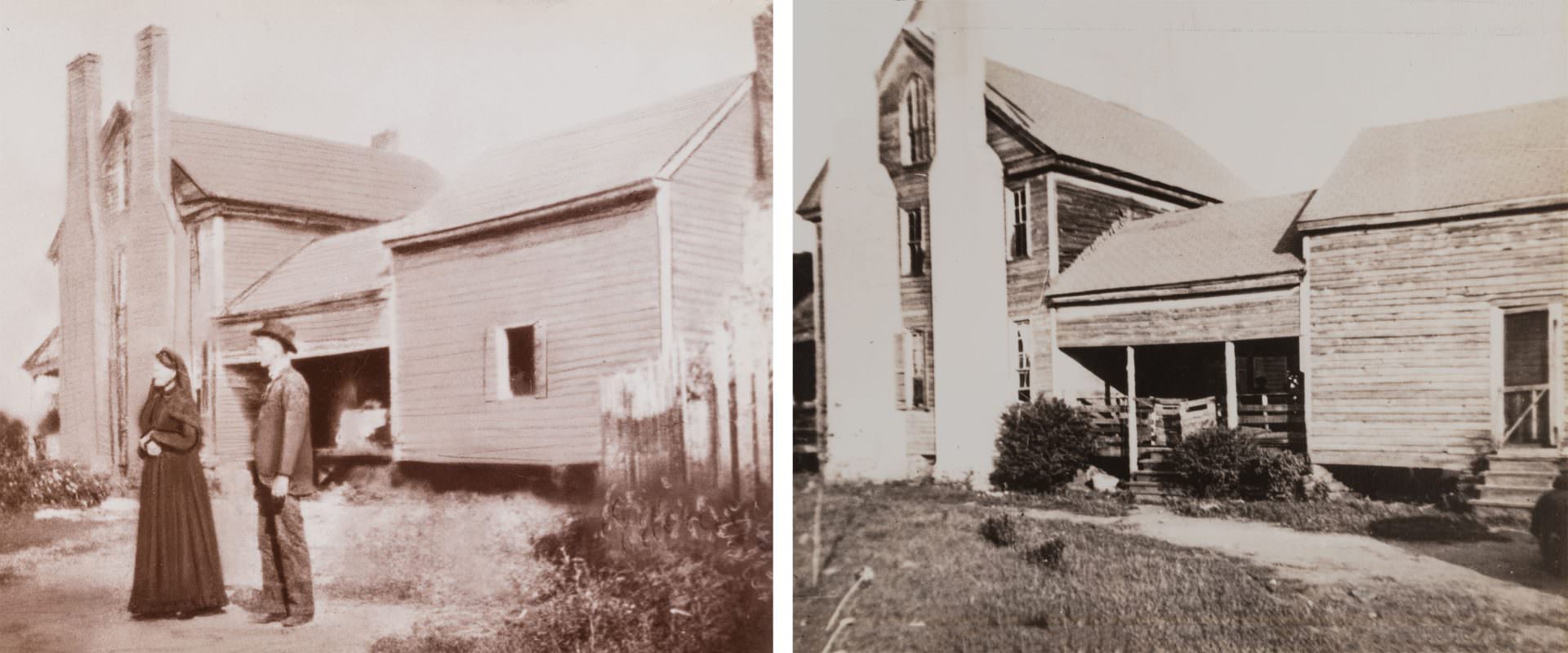
Early Photos from the Suttle Home
Building a foundation
The two-story framed house blends Federal and Greek Revival characteristics with a Victorian influence. It is very interesting to see construction methods from the early 1800’s. As seen from the pictures below, most likely this was a timber-framed construction method with mortise and tenon joints in the floor joist. During our preparation to saw the reclaimed wood floor for the cabinetry, we found hand cutnails. These cutnails had been used in the flooring to fasten the flooring to the joist. You can also see the early foundations were made using field rocks.
“The kitchen floor was our biggest challenge. We leveled and added extra supports blending today’s materials with those that were 200 years old. Matching materials was also a challenge. I had a strategy planned out to match the rock for the foundation and had made various visits to rock yards across western NC. Nothing seemed to click until the Owner took me to the edge of the pastures where we found rocks that had been cleared from fields long ago. We even found some with live moss that made it into the foundation.”~ Tony Brooks, GC Beam, Edwards, and Brooks
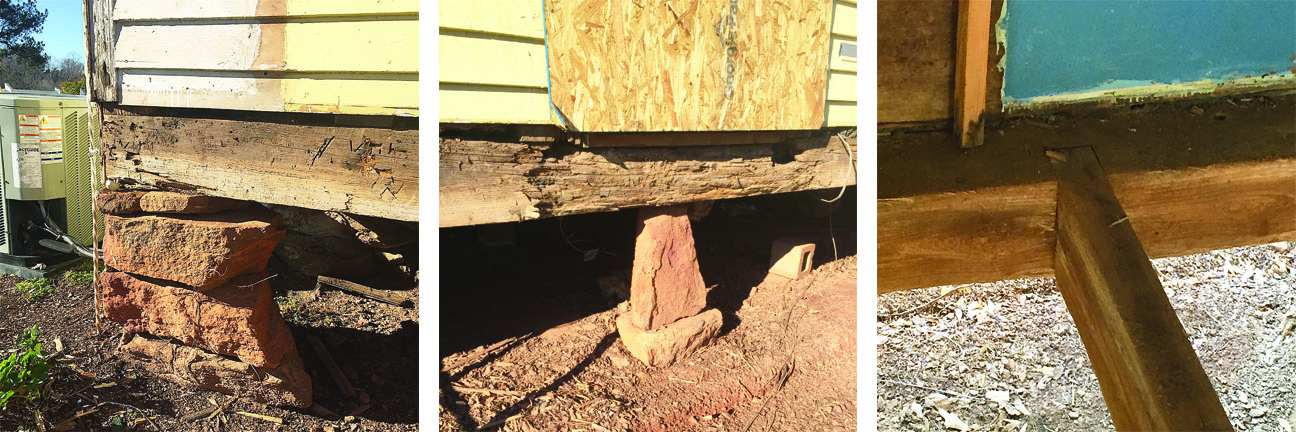
During tear out photos. The original foundation was reinforced during construction.
Using reclaimed heart pine
Working with reclaimed wood presents its own unique challenges. Questions arise such as, “Do we have enough material to complete the project? Will we be able to find a suitable match if we do not?” These are just a few issues we faced from a production perspective”. The Arey’s were former clients of Walker Woodworking, we have collaborated on several projects and we knew this would be a ‘labor of love” to accomplish. Nevertheless, Travis Walker, owner of Walker Woodworking, was eager to take on the project.
“We mostly work with brand new lumber that comes in clean and ready to use. The majority of my employees had never worked with old growth pine and had only heard of it. I had the pleasure of educating them on exactly what old growth was and what the term meant. Some were fascinated by it and just knowing the deep history of the home made it that much better. The easy part was the nails and bolts we had to remove. We scanned the wood with a metal detector. The hard part was the amount of pitch and resin in the wood. This was tough on the knives, blades, and sandpaper, and very hard on my machinery. The end results show what can be accomplished by a talented and dedicated team. ” ~ Travis Walker, Owner Walker Woodworking
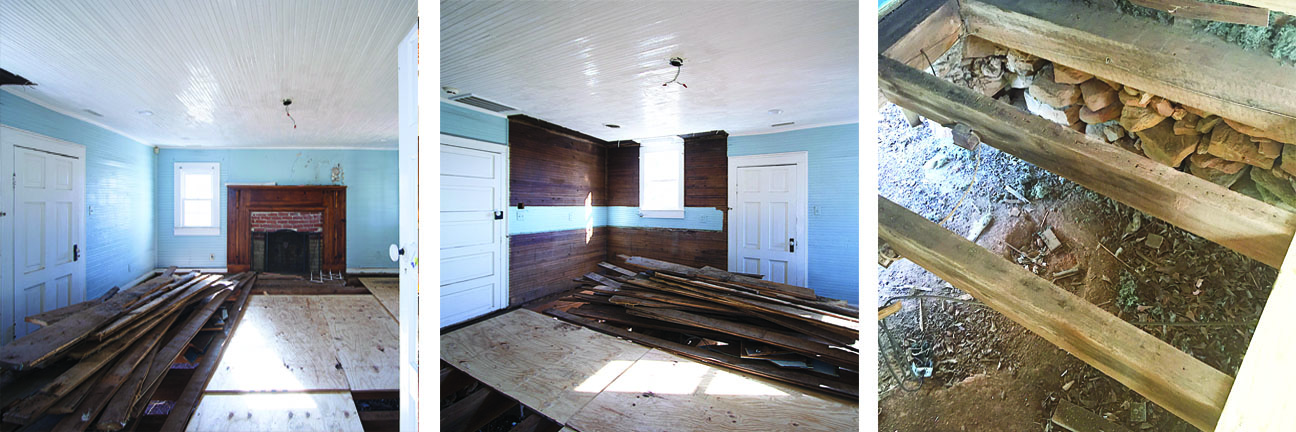
Old flooring was used for the construction of the cabinetry, and hardwoods in the kitchen and bedroom addition.
“I had the pleasure of picking up some of the extra reclaimed pine we needed to complete the project. Some of it was resawn beams that came out of the old Double Shoals Mill near Lawndale, NC. Some of those beams were over 20 inches wide and 20 feet long, which means that the trees had to be 200-300 years old at the time of harvest. If the mill was built in the latter part of the 19th century, that means those trees were growing in the early 1600’s or perhaps even the late 1500’s, the same time period that the famous Lost Colony was founded in NC! I would certainly guess that English settlers had not made it as far west into North Carolina as Cleveland County when many of these trees started growing.” ~ Justin Webb, General Manager, Walker Woodworking
Kitchen and Bath Design Challenges
Working with a historic home created a few design challenges for our design team at Greenbrook Design (LINK). The fundamental part of the floor plan had to remain close to that of the original home. Although the home had been updated several times throughout the years, we felt that we were able to keep the design as close to the original floor plan as possible also allowing the homeowners to expand cabinetry storage and function for a full working kitchen for the 21st century.
“The opportunity to work in a historic home was a unique endeavor that gave us the opportunity to be creative in establishing a new functional space. The challenge was for us to stay true to the character of the home. A great deal of family history and emotion was embedded in the project that remained as the foundation of collaboration between the contractors, designers, and homeowner. This allowed a narrow and specific route to achieve an outstanding design and allowed my team to diversify our skills in cabinet design.” ~ Brandon Fitzmorris, Lead Design at Greenbrook Design
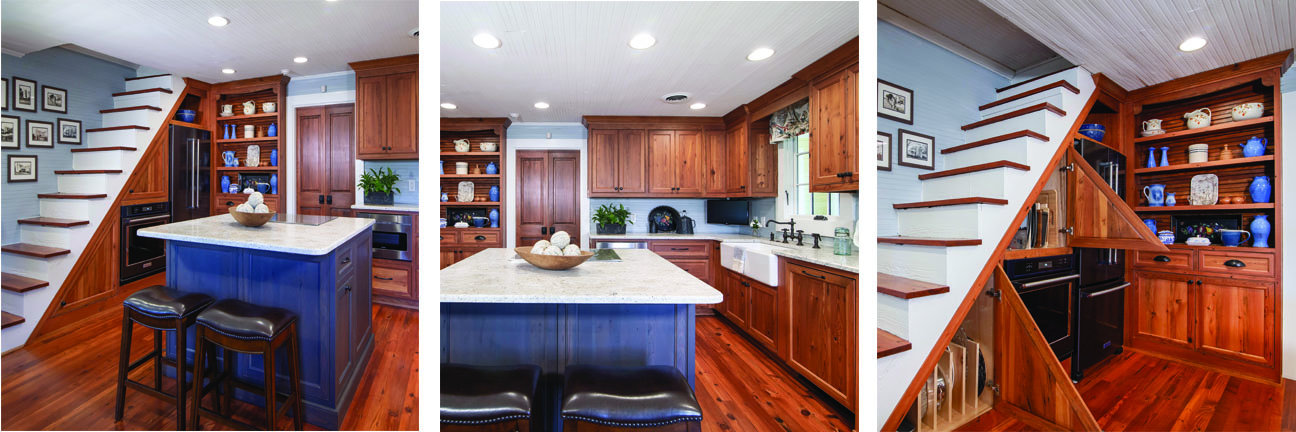
Completed Kitchen Remodel (renovation photo credits: Electric Films)
Interior Design Challenges
Wendi Gragg was involved in many components of this project collaborating with our the team meeting the requirements of the historical rehabilitation. The home remains listed with the registry of Historical Homes in North Carolina.
“The original architecture of the home was a mix of Federal, Greek and Victorian styles with several renovations throughout the years. I wanted to make sure the interiors remained rooted in a serene country spirit and that it retains the provincial charm that was indicative of the time. It was great to work with a team that you trust and depend on to meet the highest level of craftsmanship.” ~ Wendi Gragg, Interior Design

Original Fireplace, Farmhouse Sink, New addition Master Bathroom.
We have many more photos that we would love to share with you, follow this link to view the full gallery.
For more design details about this project, you will find more detailed information in this link.
For more information about the home, here are available resources: National Registry Listing
Are you ready to start your remodel project? Give us a call today and we will get the process started. Our process incorporates the time each project takes, a full design package, attention to detail and a partnership with you to ensure every job is even better than what you expected. Contact Us
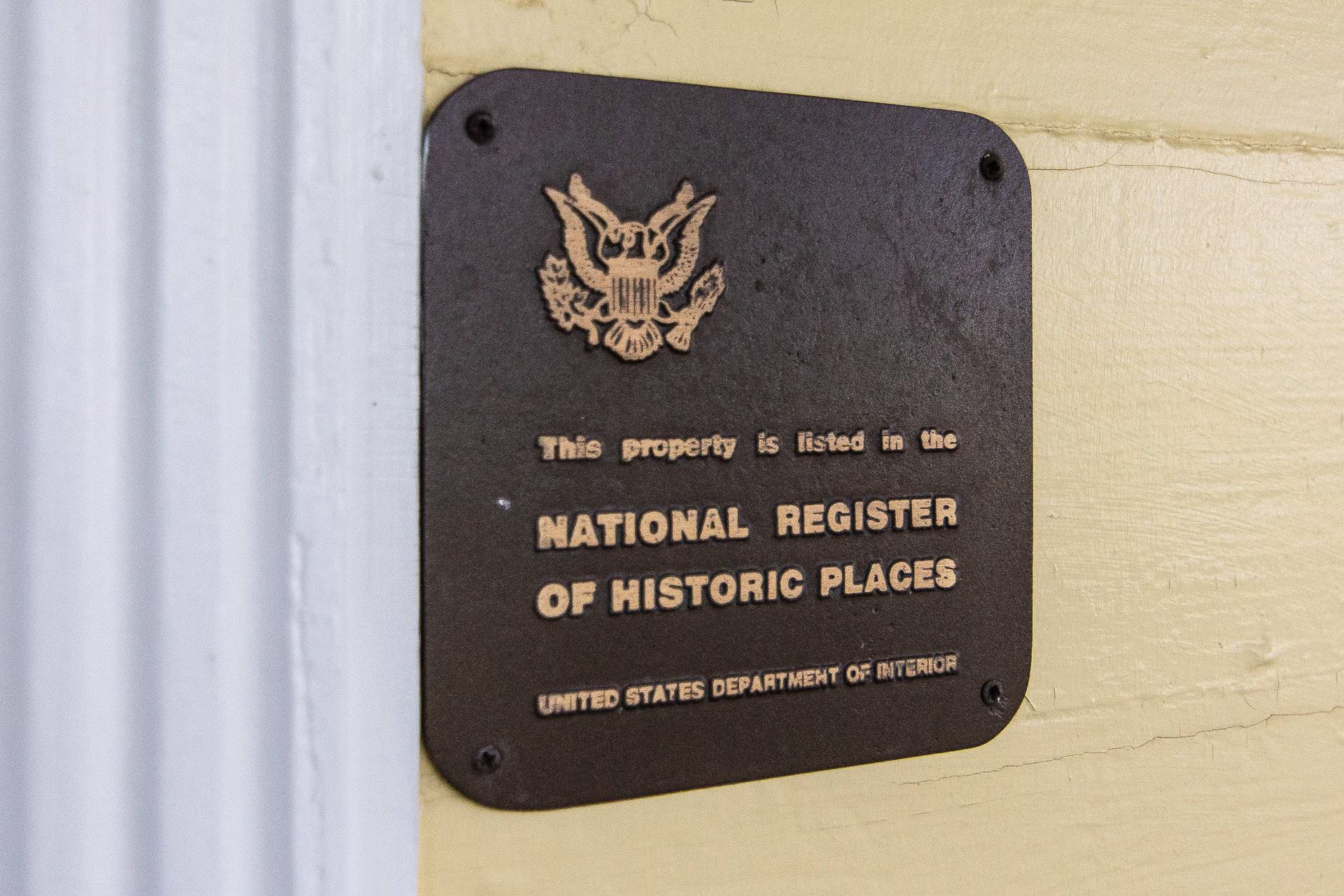
National Register of Historic Places, Joseph Suttle House